Kathleen Sharp’s legacy of Lean
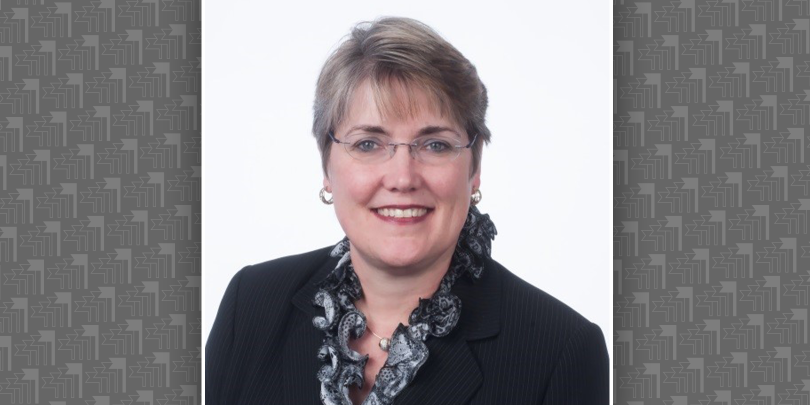
Kathleen Sharp (MBOE ’15) was a Lean thinker before she even knew what the term meant.
Growing up in a house filled with engineers — her father and three brothers shared the profession — Kathleen remembered learning the language of flow and process.
“As a kid, my family jokingly called me a ‘pretend-gineer’,” she said. “I just thought everyone did flow charts on their kitchen tables.”
A lifetime later, those early lessons — strengthened by a professional career dedicated to process improvement — would help Kathleen navigate a challenge for which there was no solution: terminal cancer.
Learning Lean
When she began a career in health care 30 years ago, hospitals and doctor’s practices were independently run. Kathleen’s responsibility was supporting their core business strategies and operations and overseeing how these impacted clinical patient care.
“In the past, health care was much more provider-centered, not patient-centered,” she said. “My guiding star has always been to not lose sight of the patient. Being in health care is fulfilling for me as I can see outcomes and improvements and know that I am helping put more of a focus on the patient.”
In the early 2000’s, while employed at a hospital system, Kathleen was chosen as one of six employees to put in place a new process improvement system called Lean.
“I introduced Lean concepts at the hospital by using everyday language,” she said. “I always want people to feel they are partnering with me. It is very important to connect and continue building those relationships throughout the process.”
With a desire to learn more, Kathleen discovered Fisher was the only college offering operational excellence with a Lean Six Sigma approach. She enrolled in the Master of Business Operational Excellence (MBOE) program in 2014, where she began learning how to help organizations foster continuous improvement and a commitment to its purpose among its employees.
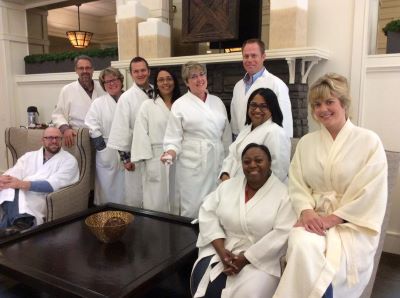
“The MBOE and Lean Six Sigma gave me the skills to improve care teams by encouraging employees to be their best by engaging everyone they encounter, including suppliers, other healthcare workers and patients,” Kathleen said.
After earning her MBOE degree, she served in various roles of performance innovation, optimization and assessment before being named the senior lean business leader at Atrium Health in Charlotte, North Carolina, where her focus was on virtual health options, population health and innovation, lean transformation and unique ways to impact the community’s health.
Applying Lean to the pandemic
At Atrium, Kathleen was thrust into finding solutions and strategies that directly affected the community during the pandemic. Her first step with her team was to develop plans to eliminate delays in patient vaccination.
“Because of our use of Lean to design systematic processes, we were able to vaccinate individuals every four-and-a-half seconds,” she said. “We were so successful in our operations that we created a playbook we shared with the White House and governors to implement.”
They thrived because the clinicians who would be doing the work were involved — a fundamental of Lean.
“We worked with frontline nurses, pharmacists and doctors to develop the system,” said Kathleen. “We discussed what to communicate and when and ways to make the process easier. Lean and Six Sigma helped build in the consistency and reliability that was needed to be successful.”
Outside Atrium, she started exploring how she could help with the high demand for face masks. Lean gave her the ability to think the outside the box.
A scuba diver, Kathleen wondered if full-face dive masks could be retrofitted for health care. She worked with a dive supplier, an Italian mask producer, a safety prevention team and the North Carolina School of Engineering to adapt and safety check the masks. Through their efforts, the team retrofitted 800 masks for use by respiratory therapists.
“If it weren’t for Lean and Six Sigma, an idea like the scuba masks would never see the light of day,” she said. “Lean gives you more brain space to be creative.”
But for Kathleen this wasn’t enough. She approached a neighborhood sewing group about making masks, provided them with a simple pattern and standards to follow, and the group came back with ideas on how to improve the process. In one weekend, six women made 800 masks and then recruited an additional 1,200 individuals to help. In six months, they produced over 70,000 masks for her community.
A Lean legacy
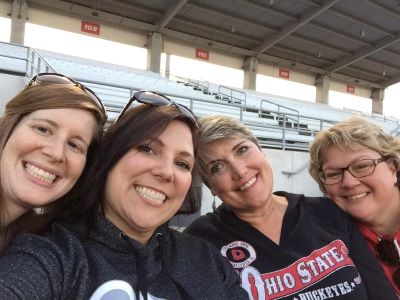
As the pandemic wound down, Kathleen began considering the lasting impact that she and her experiences could have on others. She volunteered to become a coach for the MBOE program.
“It was great to have a seasoned coach that was my encourager, asked questions of me, the organization and the processes I was working on to help me get to the root cause of an issue and correct it,” Kathleen recalled of her time in the program. “I wanted to provide the same guidance to current students as well.”
“It was such an honor to be a MBOE coach and to be able to give back to the program, even if for a short period of time.”
Even as her health declined in early 2023, Kathleen leaned into Lean more than ever. Like the flow charts in her childhood kitchen, she created tables to track her medications and cancer trends, partnered with her hospice caregivers and even created signs to visually communicate to neighbors on days she wasn’t feeling well.
“Right now, I am in the legacy part of my career and life,” Kathleen said just a few weeks before passing away from Stage IV colon cancer at the age of 62. “So many people need to learn about Lean.”
Her legacy and love of Lean will continue to pay forward even after her passing with the establishment of the Lean Into Leadership Health Care Scholarship Fund at Fisher. Created after her cancer diagnosis, the fund will help ensure future health care administrators learn Lean Six Sigma and develop the quality improvement skills that can transform an organization.
“The best advice I can give prospective students is to remain curious, continually learn and remember to speak the language of the people,” she said. “Most importantly: Don’t be the expert, be the partner.”
What is Lean?
Lean is defined as a set of management practices to improve efficiency and effectiveness by eliminating waste. Lean creates more value for customers with few resources in every business and every process.
The best advice I can give prospective students is to remain curious, continually learn and remember to speak the language of the people. Most importantly: Don’t be the expert, be the partner.