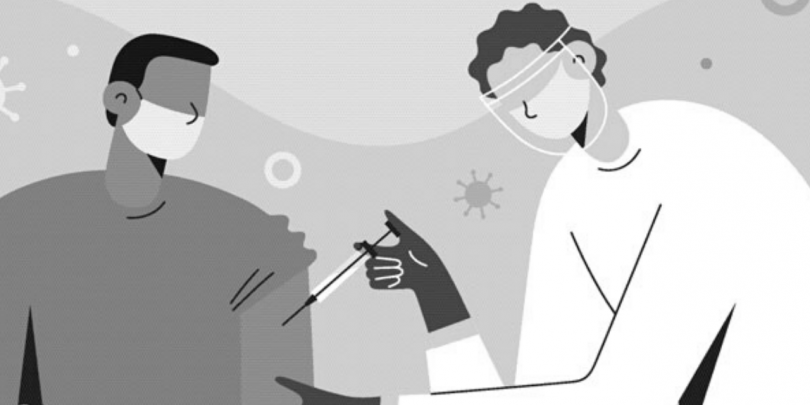
How Lean Thinking and Practice Helped Put Shots in Arms, Part 2: Wind-Down and Reflection
This note is the second of two focusing on the design and management of a single, mass vaccine delivery site at the Ohio State University Wexner Medical Center (OSUWMC) and examining the contributions of lean thinking and practice to the cycles of design, fulfillment, and use in this one site. Read part one, "Building the Process," which describes the design of the new mass vaccination system and its rapid ramp-up to high volume.
The Ohio State University Wexner Medical Center (OSUWMC)in Columbus, Ohio, a metro area of more than two million, was tasked with safely vaccinating as many individuals as vaccine supply and space would allow. Although providing vaccinations was far from new to OSUWMC, both the massive scale and the immediacy of the community need were different.
The population in Central Ohio is demographically diverse and includes many people with vaccine hesitancy. Therefore, the quality of the experience itself was paramount, requiring convenient scheduling and a fast, pleasant, and safe injection process. Process design began in November 2020 for a rapid ramp-up that would start in late December. (Two of the authors of this note, Ryan Haley and Crystal Tubbs, are primary architects of the process.)
Winding Down Mass Vaccination
In the span of a few months, the mass vaccination system accomplished what was necessary—administering over 220,000 doses of vaccine to people safely and quickly. That success was the product of hundreds of experiments performed close to where the work was done by those doing the work. However, the number of people requesting appointments began to diminish, and mass vaccination was no longer the best way to provide vaccinations. So, the focus turned toward phasing out the intense mass vaccination process, which was part of the plan from the beginning.
The same team that built the mass vaccination system also designed its successor: a new system that provided vaccinations in smaller, more variable numbers closer to where people in the community lived and worked. The team chose five sites spread throughout the community: four were associated with OSUWMC ambulatory care facilities, and one was located on campus, primarily to serve the large population of Ohio State students, staff, and faculty. Much of what had been learned during mass vaccination could be translated directly to the smaller clinics.
Reflecting on the Lessons Learned
Reflecting on the rapid design, use, and phase-out of mass vaccination at OSUWMC, we identified four overarching operational lessons from the mass vaccination experience.
- It’s necessary to find time for reflection: Rapid experimentation through numerous plan-do-check-adjust (PDCA) cycles characterizes much of the process development and improvement described in this note. The great urgency of the mission can make it easy to gloss over the careful study implied by the “check-adjust” part of the cycle, causing experiments to become trial and error without gaining much insight. One of the most significant contributions of lean thinking is understanding the importance of reflection, and an essential aspect of lean practice is finding the discipline to enact reflection. It is also important to reserve time for the leadership team to reflect on how things went; think through successes, failures, and near misses; and capture the intricacies of the operational details before they slip away. Time must also be found to share and compare reflections with leaders from other medical centers who faced many of the same problems setting up their mass vaccination processes. In that way, we can begin to identify practices that work particularly well for the all-too-likely next event.
- Standardized work works: Good scientific and evidence-based knowledge existed about the safe handling of the vaccines and their delivery to patients. The challenge was to develop standardized work that would assure that the process by which patients would receive the vaccine was indeed safe and efficient, ensuring the site could deliver the many vaccinations wanted by the population at record speed. Achieving these goals required asking healthcare professionals who were familiar with the basic knowledge but inexperienced with high-volume vaccination to execute the process as designed flawlessly, without ever harming a patient. The only way to accomplish this was by developing standardized work with the frontline workers and supporting them with both visual cues and trained, available leaders who could help if there was a problem. Further, when experiments suggested a process change, that change was captured in revised standardized work, and workers were trained on each revision at the beginning of the session huddle. This description of the necessity for employing standardized work may be “Lean 101,” but it is often not followed in practice. In particular, when the process is temporary in the sense that it will be supplanted once enough shots are given, the temptation could be to count on the professionalism of the staff rather than enacting a clear standard way to work. Thus, lean thinking and practice prevented such shortcuts and, in so doing, contributed to the successful implementation of mass vaccination. The lingering lesson is that the time spent developing standardized work is well worth it, particularly in such a high-volume, zero-defect situation.
- A daily management system is vital – if you don’t have one, invent one: Although a daily management system of tiered huddles was not universally practiced at the OSUWMC, such a system was developed for the mass vaccination process. A daily management system was critical to establish two-way communication at a regular cadence in an environment of rapid change. The management system also provided a forum for workers to surface problems and for teaching and coaching at all levels, particularly regarding the frequent changes to standardized work. In addition, it facilitated understanding and communicating progress and shared accountability. Significantly, that the vaccination team built the daily management system in an ad hoc manner didn’t diminish its usefulness -- it still filled the very tangible needs of the mass vaccination system as a whole. We have seen many instances at several other medical centers where the stress on systems caused by Covid-19 reinforced the importance of a functioning daily management system to strengthen communication between frontline workers and leaders and imbed and sustain process change. In this instance, the lesson is about the criticality of systematic daily management. It is much better to have a working system in place than to build from scratch under duress.
- Lean thinking and practice solve problems: We often think about lean thinking and practice in the context of transforming an organization for the better. In fact, the Lean Transformation Framework has become a way for many of us to understand the essence of lean thinking and practice. The framework focuses on five key ideas about a lean work system: the situationally defined purpose, the process to be used, the capabilities required, the management system needed to make it work, and underlying (cultural) fundamental thinking.
The mass vaccination problem faced by OSUWMC was not focused on organizational transformation. Rather, the urgent need was to save lives by pulling together a temporary system with many moving parts that would safely vaccinate thousands quickly and relatively conveniently. However, building the mass vaccination system did employ lean thinking and practice. Indeed, it touched on all of the elements of lean transformation: purpose, process, capabilities, a rudimentary management system, and, to a lesser extent, the cultural aspects of basic thinking.
The lesson learned is that lean thinking and practice can make a big difference even when a transformation is not the goal. The job of creating a mass vaccination system for OSUWMC was certainly made better by applying lean thinking and practice. The experience gained also serves as a powerful and specific demonstration to all involved about the power of lean thinking.
Reflecting on What We Learned
The mass vaccination process at OSUWMC was in place for only about six months. Although its time was short, its purpose was significant, and it accomplished that purpose. The evidence is the more than 220,000 doses safely put in people’s arms. As lean thinkers, we celebrate the outcome but are just as concerned with the process that led to that outcome. We have noted the contributions of lean thinking and practice to develop that process and reflected on some of the lessons that we all can take away.
Our purpose was not to describe best practices—that will come as we reflect on the experiences of those who designed and built the many mass vaccination sites in the U.S. and globally. Instead, we focus on the insights accumulated from examining the experiences gained at OSUWMC, as a team applied evidence-based medical knowledge and lean thinking and practice to an enormous, consequential problem and resolved that problem in a way that saved lives.
This article was written by Dr. Peter Ward, retired Fisher College of Business Professor, Ryan Haley, Senior Director of Ambulatory Services at The Ohio State University Wexner Medical Center, and Crystal R. Tubbs, Associate Director of Pharmacy at The Ohio State University Wexner Medical Center.