Blog Posts
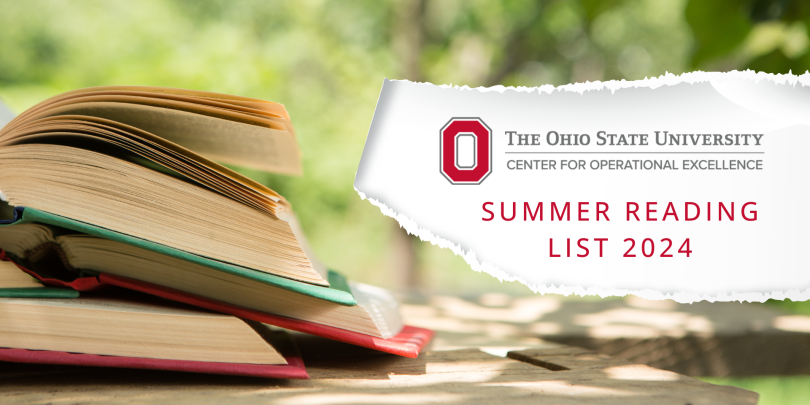
As the days grow longer and the pace of summer offers a chance to recharge, it’s the perfect time to grab a book and invest in your personal and professional development. Searching for your next great read?
The Center for Operational Excellence has turned to our recent speakers, board members, and trusted friends to present this COE Summer Reading List to our community of OpEx practitioners and problem solvers. Thoughtfully curated, this collection spans the critical themes of leadership, strategy, and continuous improvement.
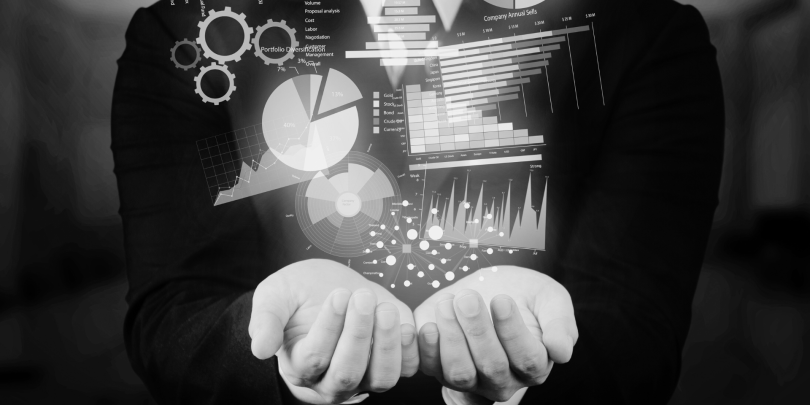
At the Center for Operational Excellence, we're committed to helping your organizations develop the skills to make data-driven decisions, transform products and processes, and maintain a competitive edge. The ability to effectively analyze, interpret, and present data is an indispensable skill for OpEx leaders and process improvement practitioners.

Our ability to change with intention requires well-informed awareness. This applies to change ranging from personal to organizational to societal. Intentionality requires us to pause, scan and be aware of the ecosystem surrounding us as individuals and collectives. The PESTLE Analysis tool is one of my favorites to leverage for a well-rounded pause and resulting analysis. It helps elevate the daily boots-on-the-ground experience to a more macro-level view of our current and emerging circumstances.
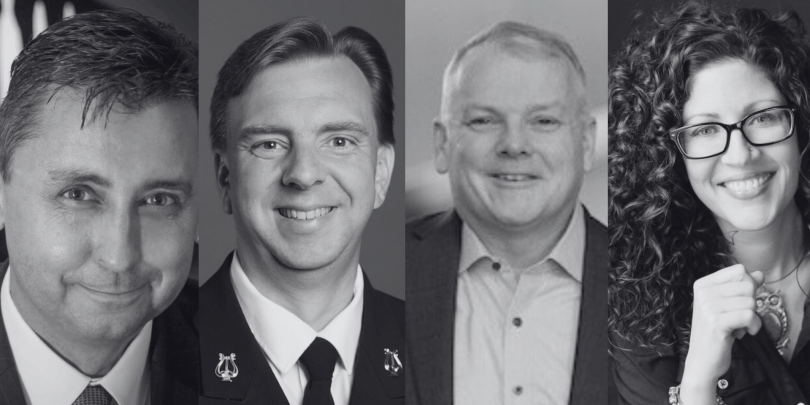
In today’s dynamic business landscape, success hinges on the ability to move from strategy creation to execution. It’s time to ignite a culture of action and excellence.
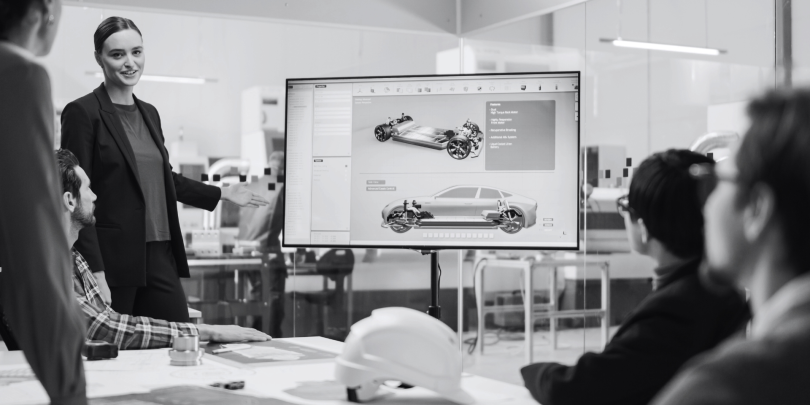
Many companies face significant challenges in meeting cost targets. Whether they're fledgling start-ups or established conglomerates, companies often encounter a familiar scenario: as their product launch draws near, they are caught in a struggle to reduce ballooning costs. Despite efforts, companies often find themselves compelled to raise prices or compromise on product quality to meet revenue and profitability targets.