Category: Lean thinking
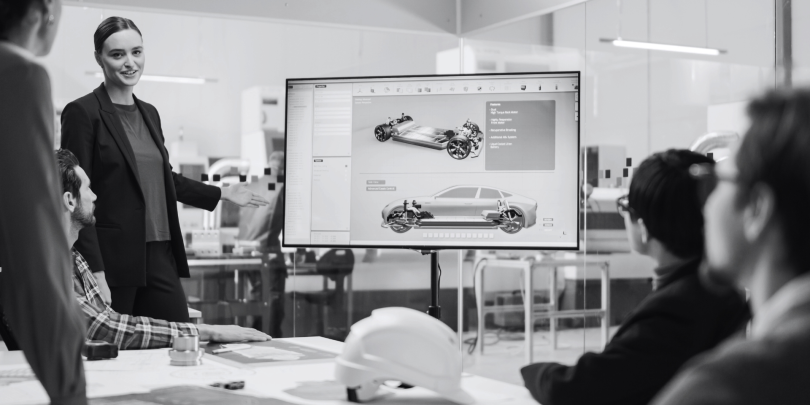
Many companies face significant challenges in meeting cost targets. Whether they're fledgling start-ups or established conglomerates, companies often encounter a familiar scenario: as their product launch draws near, they are caught in a struggle to reduce ballooning costs. Despite efforts, companies often find themselves compelled to raise prices or compromise on product quality to meet revenue and profitability targets.
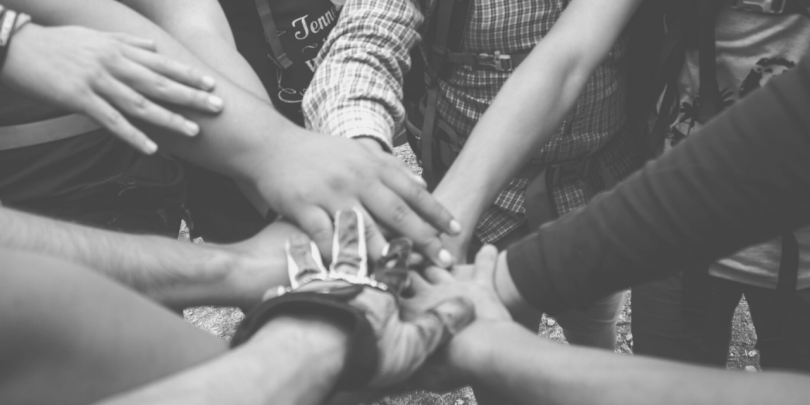
The good news is we live in a world of unprecedented opportunity. If we can’t do it ourselves, we can collaborate with someone who can. The bad news is though anything seems possible, everything is not. If we want to be good at something, we need to focus. Regardless of “what” you choose to collaborate on, operational excellence has some ideas about “how” you do it. Let’s focus on that by taking a quick look at 5 reasons why operational excellence is so important in a collaborative world…
1. Value is the gold standard.
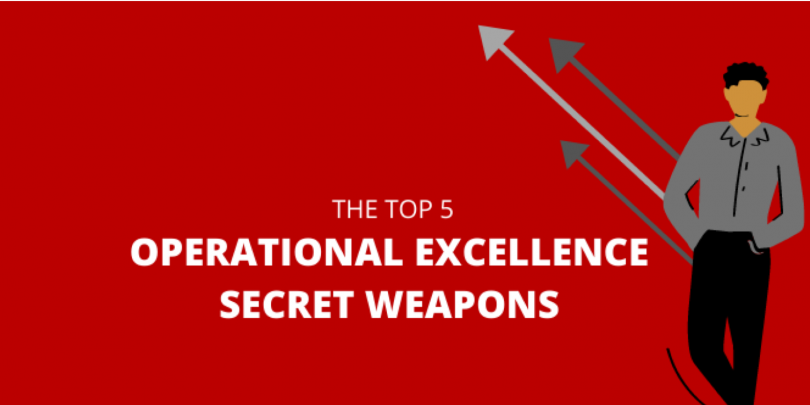
Tracy Owens is a business transformation leader who has led his employers and client organizations in developing a culture of continuous improvement to achieve near-term objectives and better long-term results. Tracy has a deep toolbox for process improvement and a wide range of experience, interests, success stories, and connections. We asked Tracy what his top 5 secret weapons are when it comes to OpEx tools.
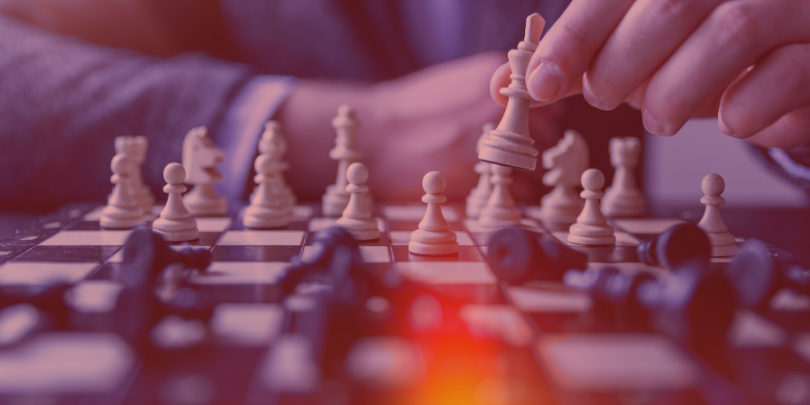
I recently had a conversation with a veteran operations manager about his new company and its plan to deploy a lean strategy. In fact, I often hear lean thinkers describe lean as a strategy. But is it? Lean thinking and practice certainly is strategic in the sense that it is an all-encompassing approach to running a business.
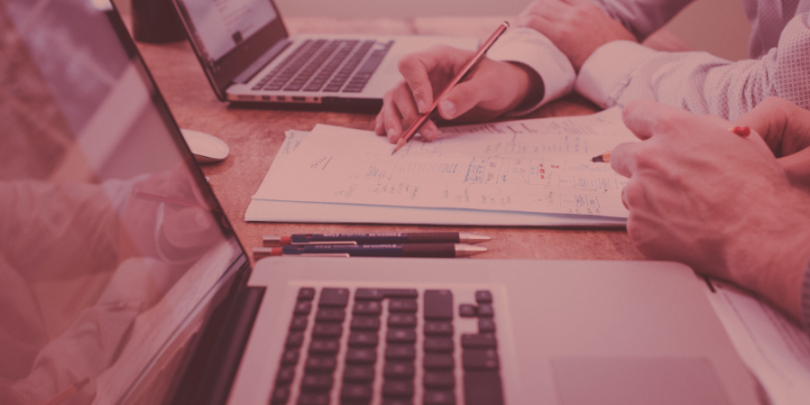
I was reading yet another article on leadership responses to the COVID 19 pandemic on the importance of “purpose”. The “why” most call it. For example, “Leading with purpose and humanity” was the headline in an article on McKinsey’s interview with Best Buy CEO, Hubert Joly. It got me thinking about “why” we embrace Operational Excellence and “why not” look at it a little differently.