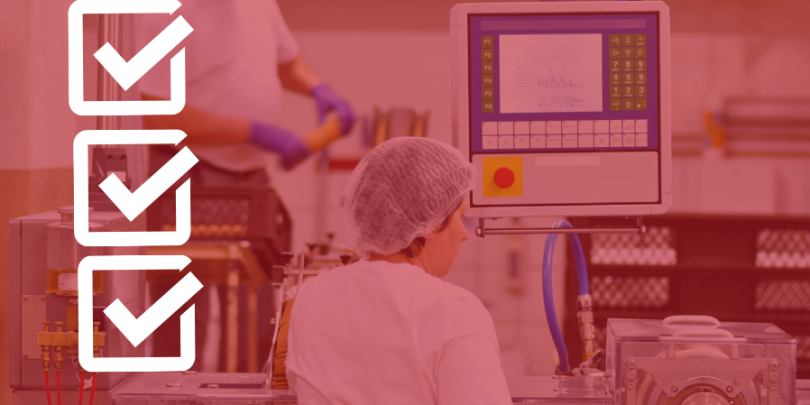
Routines With a Backbone
The COVID-19 crisis has undoubtedly shifted our lives in a myriad of ways, including how we work. While more than twenty percent are out of work due to COVID-related layoffs, the global pandemic has forced the eighty percent still working to either perform their responsibilities remotely or to work in a facility while trying to maintain social distance (along with additional new best practices like increased sanitation or shift staggering). Regardless of where we are doing our work, one thing is certain: we have all had to adapt. As we begin to unfreeze work routines, now is the time to rethink them.
Routines are defined simply a sequence of repeated activities, but there is great benefit in the performance of routines. Routines allow us to improve at tasks, reduce the stress associated with complexity and newness, and help us cope with other change by remaining constant. In addition, following routines prevents us from the “goofing up” that happens when we do things out of order. When faced with forgetfulness or complexity in our routines, we often write down notes or reminders. In fact, pre-flight checklists for pilots were introduced as a safety device in the 1930s when the list of pre-flight items became too long to be consistently remembered by pilots. Following a checklist prevents skipping a step or doing one out of sequence by documenting a routine and adhering to that documentation.
Conformance to the documentation leads to consistency and, in turn, quality. However, true standardized work is much more than developing and following rules. Problems that are uncovered when following the prescribed method lead to problem solving at the point where the problem occurs and, through experimentation, revision of the standardized work. In this way, countermeasures are found by the people closest to the work and tested experimentally. Once shown to be effective, those countermeasures are incorporated into the standardized work. To be effective, standardized work needs to extend throughout the operating system so that individual activities are tightly linked through standard connections and pathways. (Steve Spear and Kent Bowen’s classic 1999 Harvard Business Review article “Decoding the DNA of the Toyota Production System” provides a terrific exposition on this point.)
Specifically, standardized work imposes a standard— the content, sequence, timing, and outcome of activities. In addition, standardized work includes rate of demand (Takt) and it establishes a standard work-in-process inventory level. Where a checklist documents the proper sequence to be followed, standardized work requires significantly more information. Using that additional information pays a big dividend in our ability to surface problems where they occur and to resolve those problems more quickly by getting to the cause and introducing countermeasures experimentally. Most important, problems are resolved in a way that improves the process by improving standardized work, thus incorporating a feedback loop that captures learning.
Often overlooked in discussing standardized work is the fact that it should be largely developed by the people who do the work. Further, it should be frequently changed, following a controlled process and as an experiment with participation from those people who do the work. In this way front-line workers are continuously engaged in both doing work and improving work. To overlook the worker in developing and improving standardized work is really to miss the point.
As an example, I offer a study by some colleagues on kidney transplant patients. The problem was that hospital readmissions within 30 days by transplant recipients was higher than desired. Research indicated that the cause was patients’ difficulty with following post-operative recovery regimen at home after discharge. Further study pointed to variability in the post-operative patient teaching as a possible root cause. The transplant nurses who did the patient training recognized the problem and were eager to develop and adhere to standardized discharge work. Over a period of weeks, the nurses reviewed the various training aids and printed instructions as well as the teaching methods used in the context of evidence-based guidelines. It was also noted that patient handoff to an outpatient post-transplant clinic where further patient training occurred was also a source of variation. Eventually, outpatient nurses also joined the study team. With facilitation by the researchers and approval of the administration, the group developed standardized discharge work for teaching post-surgical transplant patients both in the hospital and after they transitioned to outpatient care. The group also developed standardized work for the transition or handoff from hospital to outpatient-based care and teaching.
In this example, standardized work specified content, sequence, timing, and outcome. It also specified the capacity limits and the number of patients in-process. No changes were made in surgical processes or other clinical procedures. The results were dramatic. The unit achieved and sustained a 32 percent decrease in 30-day readmissions. At the same time, patient satisfaction scores increased significantly. Again, the only change was in developing and following standardized work.
Sustaining the standardized work also required some new behaviors. Patient teaching became a regular agenda item at huddles and bi-weekly joint huddles between inpatient and outpatient nursing teams were instituted. When problems occurred, they were studied and countermeasures were developed. Teaching standardized discharge work to nurses new to the unit became part of on-boarding. Nursing and other clinical leaders checked and encouraged periodically.
The moral of the story is that routine non-production activities can benefit greatly from real standardized work, developed and sustained by the people who do the work. The nurses who developed and sustained that standardized work were motivated by concern for the health and safety of their patients, who were returning to the hospital with too great a frequency. In a sense, they were reacting to a crisis.
As we adjust many of our routines in the midst of COVID-19 crisis, I am reminded that Churchill is said to have advised that we should never let a good crisis go to waste. It seems to me that it would be a terrible waste not to develop standardized work as we invent new ways with new routines. In avoiding that waste, we position our organizations to experiment productively to improve processes continuously. Non-production processes are particularly good candidates for standardized work. They have often been neglected relative to manufacturing processes in the past and they are more likely to be distributed, with work being done remotely. In these instances, the benefits of standardized work will be even greater because work done in isolation is likely to drift without clear standards and accountability.
Every routine deserves a backbone.